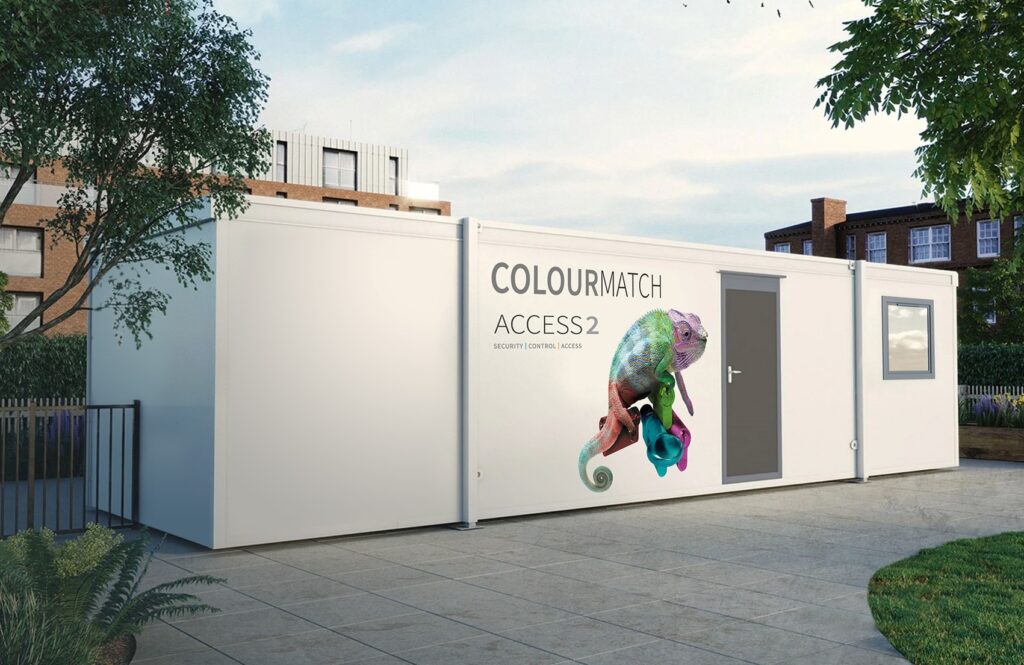
Colourmatch – The benefits of using powder coating to finish cylinders
Powder coating is a dry finishing process that involves applying a dry powder material onto a metal surface before curing it with heat. The powder material consists of finely ground particles of pigment and resin that form a protective layer over the metal surface when heated. Unlike electroplating, powder coating does not require hazardous chemicals or solvents; instead, it relies on heat to cure the powder material onto the metal surface. Additionally, because no hazardous chemicals are involved in the process, it is considered more environmentally friendly than electroplating. This is the colourmatch service that we offer to make the option of cylinder finish yours. Lets explore the benefits of powder coating:
Less Waste
When dealing with paint, any overspray is automatically discarded since it cannot be reclaimed and used again — as soon as it leaves the paint gun, it begins to dry. With powder coating, any overspray is in powder form, meaning we can capture and reuse via our water wash booth system. This means there is no need for costly or dangerous disposal units and little to no waste when powder-coating a piece of equipment. The powder used in this type of coating doesn’t dry or cure until it’s exposed to heat.
No VOCs or HAPs
The biggest environmental concern when dealing with paint is the presence of volatile organic compounds (VOCs) and hazardous air pollutants (HAPs). Paint pigments are mixed with a solvent to make them usable, and as that solvent dries, the VOCs and HAPs begin to evaporate into the atmosphere around the project. VOCs can damage the ozone layer and create health hazards for anyone who breathes them in. In a contained, nonventilated space, they will continue to accumulate, reaching dangerous levels.
While paint manufacturers have started to create low- and no-VOC formulas, these paints are not as strong or durable as those with VOCs, making them useless for protecting equipment from the elements.
Powder coating contains almost no VOCs, and since the powder itself is inert, it doesn’t release these materials into the atmosphere.
Easier to Fix Mistakes
If you make a mistake while applying paint, it’s a mess. You need to remove the paint using solvents, which contain VOCs and HAPs, before applying a new coat of paint. It’s wasteful, and it also pollutes the environment. Before a powder-coated piece reaches the curing stage — where the equipment is baked to melt the powder and turn it into an even and durable coating — fixing a mistake is as simple as wiping it off with a clean cloth and recoating it. Any removed powder can be recycled or disposed of without generating additional pollution.
A greener, cleaner choice
In general, powder coating provides a better, more durable coating that will protect your equipment for years to come. As more paint manufacturers transition to low- or no-VOC formulas, those paints may no longer be able to provide the same protection. Powder coating is quickly becoming the best, most cost-effective and most environmentally friendly choice for equipment protection and weatherproofing.
No solvent wastage hence simply more eco-friendly.
Powder coatings contain no VOCs or solvents. There is no costly wastage of solvents which at application viscosity, constitutes up to 70% of conventional liquid paints. These solvents, which volatilize during application and stoving are usually not recoverable. Legislation introduced in various parts of the world has prohibited their discharge into the atmosphere. This means in some cases, after-burners must be installed to eliminate the solvents with an added increase in costs.
No effluent disposal problems
Water wash spray booth are often used with liquid paint systems. The overspray is often emulsified in the water. This in some cases is put directly into a drain or allowed to settle out in sludge tanks. Powders do not give rise to this kind of problems and the associated extra waste disposal costs.
Powder helps reduce air pollution
Any over sprayed powder is recoverable. This is great news in reducing waste, and no powder need to escape into the atmosphere.
Powder helps reduce the health hazard to operators
As powders do not contain solvent there is a marked reduction in nose, mouth and throat irritation. Any liquid paint which comes into contact with an operator’s skin needs to be washed off with solvent, and then removed by emulsifying with soap in hot water. Sometimes even special industrial hand cleaners must be used. In general powder does not cause skin irritation though in rare cases individuals may react to certain types of powder. The powder can be removed from the skin easily by washing with warm water.
Powder offers a reduction in fire risk
There are no solvents in powder coatings this reduces the associated fire risk. It therefore gives cost savings on statutory safety features in your plant and reduces insurance premiums. You also won’t be subject to flammable liquids regulations.
Processing time is reduced
Powder processing times are generally shorter than those used for liquid paints -there is no solvent so no flash off period is required. Instead, the powder coated articles can pass directly into the oven. This gives substantial saving in space and time and energy.
Reduced energy requirements compared to solvent based stoving paints
The oven the air turnover rate is significantly reduced as there is no build up of potentially explosive solvent which must be removed. This means less heating of air and less energy consumption and lower cost.
Reduced energy requirements compared to aqueous based paints
Aqueous or water based paints also contain organic solvents. Therefore, the energy saving above associated with the removal of VOC from the coating and air in the oven can be achieved. Additionally, with aqueous based paints there is a need to control the temperature and humidity of the application area precisely which is an added cost compared to powder coatings.
Air conditioning requirements are reduced – more cost savings
The air extraction in a powder spray booth is a lot less than for solvent based paints providing economies in ventilation and the consequential heating of work areas. As less warm air needs to be replaced in workshops, less dust is attracted and there is less air-draught for the operators to contend with.
95% powder utilization
With powder, material loss can be kept to less than 5%. Any powder overspray can be recovered and the recovered powder can be blended with virgin powder to provide up to 95% utilization. Almost all of what is in the powder box finishes on the coated article. Many liquid coatings contain a high level of volatile content which is lost during the painting process meaning perhaps only 50% of what is in the tin actually ends up on the workpiece.
Powder is cleaner to use
Applying powder is much cleaner than applying wet paint. A spray booth can be cleaned down quickly and easily. Any spillages of powder outside the booth can be removed with an industrial vacuum cleaner.
A powder application plant is less costly
A powder application plant, either manual or automatic, is extremely simple to operate and less costly than a multicoat liquid system.